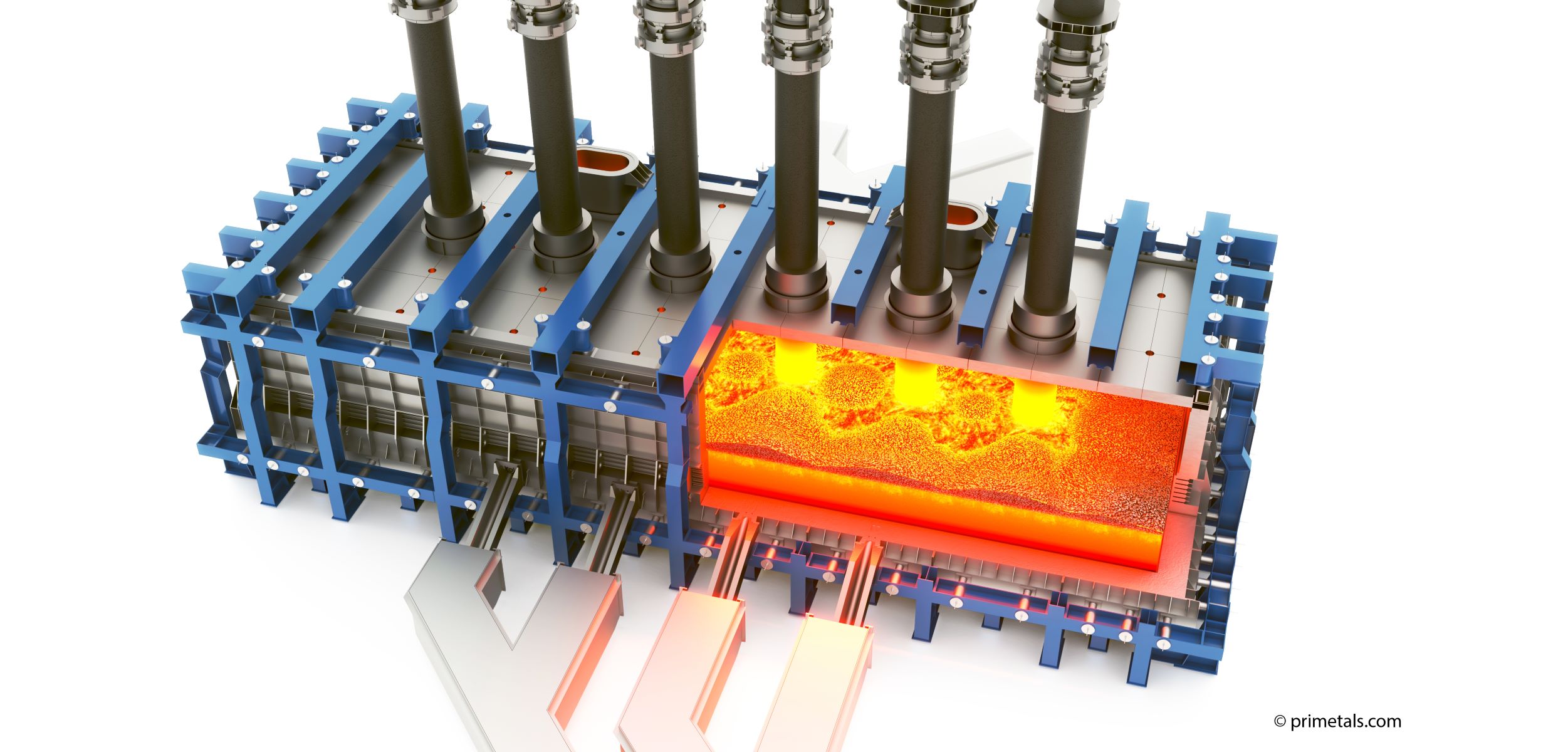
Overview
The hydrogen direct reduced iron (H2DRI) process is emerging as a key technology for decarbonising steel production. While current DRI production relies on high-grade iron ore, the anticipated growth in DRI usage means that lower-grade ores, which contain more gangue (non-metallic minerals), will also need to be processed.
Existing electric arc furnace (EAF) technology struggles with high-gangue DRI, prompting the need for an intermediate solution such as electric smelting furnaces (ESFs). ESFs can separate gangue into slag while producing liquid iron for steelmaking. Additionally, the slag generated could serve as a feedstock for cement production, adding value to the process. However, the ESF route requires further evaluation to address challenges related to productivity, energy efficiency, and operational costs.
Currently, ESF technology has been commercialised for relatively low tonnages of iron production (less than 1 million tonnes per year) and the scientific basis of these processes are not well understood. For example, it is not clear how different levels of gangue (undesirable mineral matter found with iron ore) in DRI effect the rate of smelting or influence productivity gains achieved through hot feeding of the DRI.
Using advanced modelling, laboratory experiments and industrial data, this project will provide insights into the technoeconomic viability of processing Australian iron ores through the H2DRI-ESF route. The research will build on findings from HILT CRC projects RP1.004 and RP1.005 and offer recommendations for optimising ESF technology to support a sustainable steel industry in Australia.
Project Details
HILT CRC Milestones
Research Areas
Project Outcomes
Project Benefits
Download the Project Summary